Uncovering GDP violations during audits is a crucial part of maintaining pharmaceutical quality standards. Yet, the list of discovered shortcomings can be extensive, posing significant challenges. These incidents, reported as non-compliances by
regulatory bodies, demand vigilant monitoring and strategic handling within the framework of Good Distribution Practices (GDP).
Preserving consistent quality standards is of utmost importance. But how can this be achieved effectively? The answer lies in leveraging logistics quality management software for GDP quality. Let’s see how a digital QMS not only addresses but proactively tackles quality concerns, ensuring a robust approach to compliance and excellence in pharmaceutical distribution.
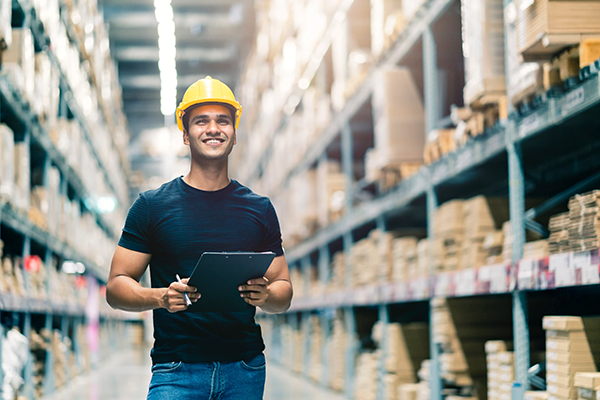
Quality Management in Logistics: identifying and addressing common deviations in GDP Compliance
- The GDP Association, an ECA Foundation Interest Group, recently shared examples of deviations documented in GDP Non-Compliance Reports:
- Inadequate storage facilities for cold chain/cool storage medicinal products.
- Failure to control temperature within specified limits.
- Negligence in fulfilling responsibilities by the designated person in charge, with no notification of a change to the competent authority.
- Insufficient verification of suppliers and their wholesalers' authorisation before purchase, lacking approval from the responsible person.
- Lack of proper checks on medicinal products for security measures and falsification, disregarding safety information provided by the securpharm system.
- Inadequate documentation of purchases and sales, both in quantity and batch records, compromising the seamless tracking of all activities.
How Corrective and Preventive Actions (CAPAs) proactively tackle deviations for Quality Management in Logistics
In fields like GDP and pharmaceuticals, continuous monitoring of the long-term effectiveness of these measures is paramount. Once a CAPA is deployed, evaluating its impact becomes pivotal. In cases where a CAPA falls short, it prompts the need for new strategies to mitigate risks promptly.
e-signatures, contributing to a seamless, accountable system.
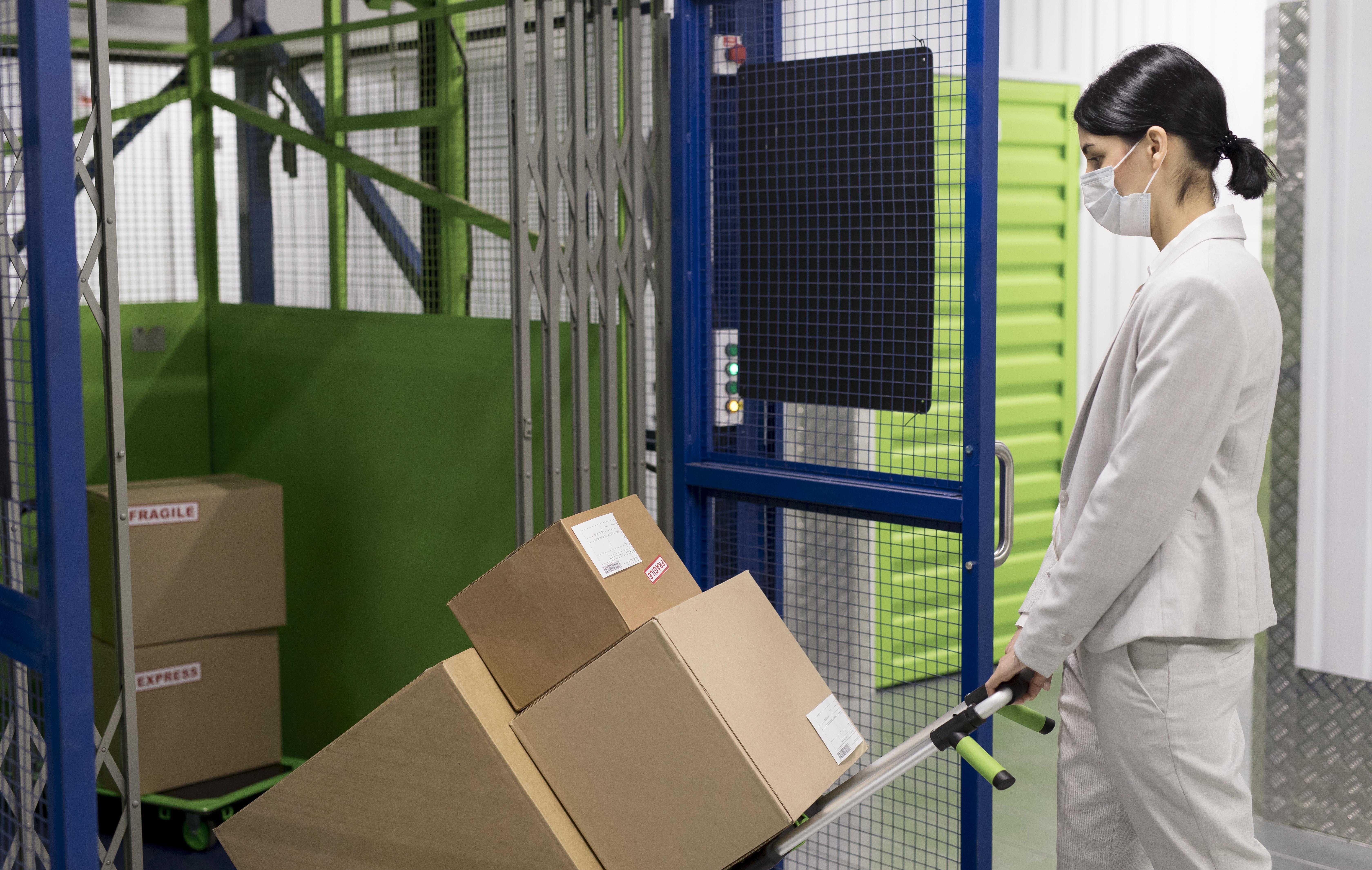
Navigating a proactive approach: embracing Risk and Change for Quality Management in Logistics
- Complete elimination of risks
- Mitigation of risks to manageable levels
- Acknowledgment and continuous monitoring of unavoidable risks
Effective Calibration Management for Quality Management in Logistics
Empowering Excellence: navigating Pharmaceutical Quality with innovative solutions for Quality Management in Logistics
So, how do we tackle these challenges effectively? The answer lies in the empowerment of Logistics Quality Management software—an innovation that doesn't just respond but proactively addresses quality concerns. This tool isn't just a solution; it's a pathway to robust compliance and excellence in pharmaceutical distribution.
You may also like: